FEASIBILITY STUDIES OF A MATRIX ASSEMBLY SYSTEM
Research project: Feasibility studies of a matrix assembly system
Research area: Simulation, production logistics, material flow
In cooperation with: Intralogistics manufacturer
Start of the project: 01/2019
End of the project: 05/2019
ABOUT THE PROJECT
The increasing variety of products in many industries poses major challenges for conventional production systems with rigidly interlinked assembly lines. This research project compares production using assembly lines with an alternative form of production, matrix assembly.
A matrix assembly system is characterized by assembly stations between which the material does not flow along rigidly defined paths, as is the case with a conveyor belt, for example. Instead, the material can take an individual path through the assembly system for each product to be manufactured and no longer follows a cycle that applies to the entire system, as is the case with an assembly line. The resulting flexibility promises to make it easier to deal with widely varying processing times and disruptions.
In order to make this comparison, the Institute of Technical Logistics is developing a parameterized simulation model for the project, which will be used to simulate and evaluate various scenarios. The focus is on the consideration of different layout variants for a matrix assembly system, as well as several control mechanisms for the material flow. For the comparison of the production forms, the productivity and the behavior in the event of faults in the assembly system are examined in particular.
In order to make this comparison, the Institute of Technical Logistics is developing a parameterized simulation model for the project, which will be used to simulate and evaluate various scenarios. The focus is on the consideration of different layout variants for a matrix assembly system, as well as several control mechanisms for the material flow. To compare the production forms, the main focus is on productivity and the behavior in the event of faults in the assembly system.
By comparing different layouts and control algorithms of a matrix assembly and comparing them with a conventional assembly line, recommendations for follow-up studies are developed and the basis for future decisions on redesigning the project partner’s assembly system is created.
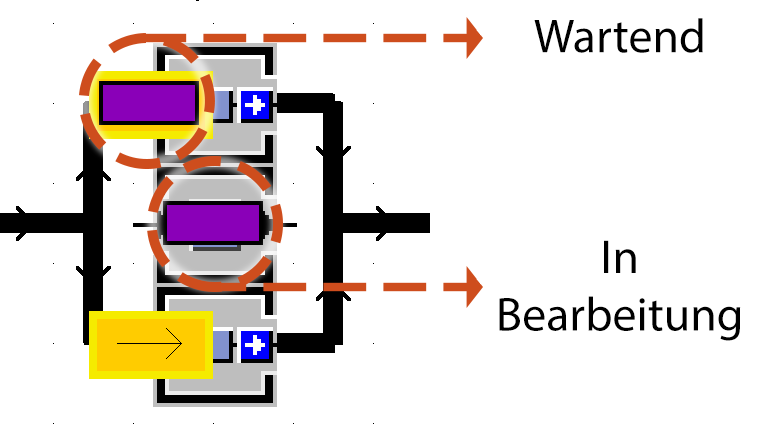