Modeling and Dynamic Simulation of Multistage Particle Separation in a Turbulent Fluid Flow
- Departments:
Institute of Fluid Dynamics and Thermodynamics, Chair of Fluid Dynamics and Technical Flow, OvGU Magdeburg
Institute of Process Engineering, Chair of Mechanical Process Engineering, OvGU Magdeburg- Project leaders:
Prof. Dr.-Ing. habil. J. Tomas, OvGU Magdeburg
Prof. Dr.-Ing. habil. D. Thévenin, OvGU Magdeburg- Researcher:
M.Sc. H. Glöckner, OvGU Magdeburg
Dipl.-Ing. C. Roloff, OvGU Magdeburg
Ultimate Goal
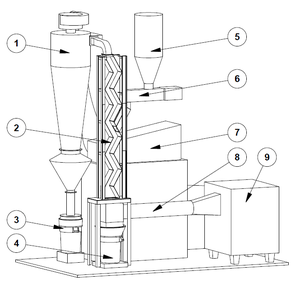
The multistage particle separation in a turbulent fluid flow is a special case of air classifying and is used in many solid processes (e.g. treatment of cement, separation of scrap cable). A schematic representation of the pilot plant is shown in Figure 1. The characteristic attribute is the zigzag shaped channel (2). The fan (9) intakes and accelerates the process air, which flows through the channel from bottom to top. The feed product is stored in a hopper (5) and is brought into the channel by a vibrating conveyor (4). During operation, coarse and dense particles leave the channel downwards as the coarse product (4), whereas fine and light particles are carried by the process air upwards into the cyclone (1), where they are separated from the air stream as the fine product (3). If necessary, a filter (7) can be employed into the loop to separate the finest fraction.
One aim of this work is to find locally and temporally resolved models describing the involved sub-processes of the system. Furthermore, models that predictively characterize the separation behavior and the process quality depending on feed material properties, mass loading of the process air, separation attributes and classifier geometry will be developed. In addition, coupled simulations of fluid mechanics (CFD, Computational Fluid Dynamics) and particle mechanics (DEM, Discrete Element Method) will be performed and validated using different measurement techniques such as PIV (Particle Image Velocimetry) and PTV (Particle Tracking Velocimetry). The process will be optimized with respect to energy consumption and process quality.
Work Program
Within the research project, multi-scaled approaches on the microscopic (particle movement) and macroscopic scale (separation process) are necessary. To achieve the challenging numerical simulations, solutions of both parts have to be combined.
On the macroscopic scale, comprehensive separation experiments will be drawn into focus. In addition to classifying (separation by particle size) of sand-gravel mixtures, sorting (separation by solid density) of soft-air-particles was performed. Finally, separation experiments with more complex mixtures (e.g. specifically formed plastic granules) will be executed with particle size, density and shape as separation attributes. Using different mass fluxes of the feed at fixed air velocities, the effect of mass loading of the process air on the efficiency of the separation operation will be investigated. In this case, the determination of the separation attribute and as well as several energetic values (such as pressure drop, energy consumption, etc.) is of utmost importance. Furthermore, the variation of the channel geometry, the number of stages and the determination of the feed stage will help to find an optimal design.
On the microscopic scale, the velocity field and the particle movement inside the turbulent flow will be investigated. In addition to measurements like the performed Laser-Doppler-Velocimetry (LDV) and Particle Image Velocimetry (PIV) to visualize the flow field, particle trajectories will be captured by Particle Tracking Velocimetry (PTV). For simultaneous acquisition of different particle collectives color coding will be applied.
The preconditions for the measurements were met by extensive alterations of the test rig. A new fan was installed for the variation of the volumetric flow rate of air. For a continuous controllable solid mass flow the screw conveyer was replaced by a vibrating conveyer. To enable optical access over the complete channel height from three sides a new modular zigzag channel was designed and built (see Figure 2). Through the modular design the number of stages can be varied with little effort.
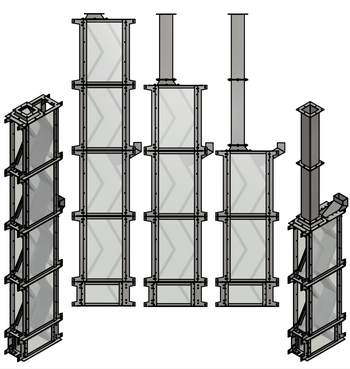
Using the determined fluid properties single-phase CFD simulations where executed and validated using the flow field measurement data to find an optimal turbulence model. In this case, three dimensional models using Reynolds-averaged Navier-Stokes-equations (RANS) and unsteady Reynolds-averaged Navier-Stokes-equations (URANS) where used. On this basis, multi-phase flows will be numerically simulated with respect to the occurring mechanisms (e.g. collisions, interactions); an increased precision will be achieved by using one-, two- and four-way coupling (Figure 3).
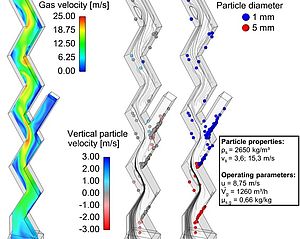
The insights already gained where used to create a dynamic separation model based on the mesoscopic particle motion by convection and diffusion. This model will be further developed as part of the subproject, so that a predictive classifier behavior estimation and optimization is possible.
Activities of the individual working groups:
WG Thévenin, OvGU Magdeburg
-
Measurement of the air flow field.
-
Characterization of the particle dynamics in the turbulent fluid flow.
-
Development and validation of the numerical simulations.
-
Execution of the numerical process optimization.
WG Tomas, OvGU Magdeburg