Development of a dynamic-physical process model for sieving
Institute: Mechanical Process Engineering and Solids Processing, Institute of Process Engineering, Technische Universität Berlin
Project leader: Prof. Dr.-Ing. H. Kruggel-Emden, Technische Universität Berlin
Researcher: M.Sc. F. Elskamp, Technische Universität Berlin
Project objective
The aim of the proposed project is the investigation of the process step sieving in continuous and discontinuous mode also under influence of varying amounts of fluids. Polydisperse particle systems involving particles of complex shape are addressed. Basic relations between the particle shape, the bulk distribution and the operating parameters as well as the screening results are examined. Especially changes in process conditions (variation of mass flows, particle distribution, operating parameters as well as start-up and shut-down processes) are considered. Based on existing models in literature, a prototype of a phenomenological process model is developed that is able to describe dynamic changes in process conditions (e.g. particle size, mass flows, particle shapes, distribution of the bulk material and operating parameters). The parameters of this dynamic model are not derived from experimental studies, but from discrete element simulations that represent the motion of all particles over time in detail and which can be coupled with methods for numerical flow simulation to consider the influence of fluids. For this purpose, a suitable discrete element framework is designed, which makes it possible to derive the required model parameters for stationary or dynamic operation under low numerical effort. The developed framework must be tested and validated to integrate it into a modular dynamic flow simulation.
Methodology and work schedule
Based on performed detailed DEM simulations of segregation processes on grate systems, an extension of the existing DEM code was developed to determine an appropriate representation of the screen surface in the simulations [1]. The DEM simulation parameters were determined and a subsequent testing of the simulation framework based on an experimental study of a screening process from literature was accomplished [2]. On this basis, discontinuous sieving processes were considered under steady state and time-varying conditions [3,4]. In these examinations only the processes of particle segregation and particle passage occur (compare Figure 1).
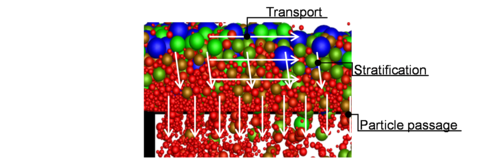
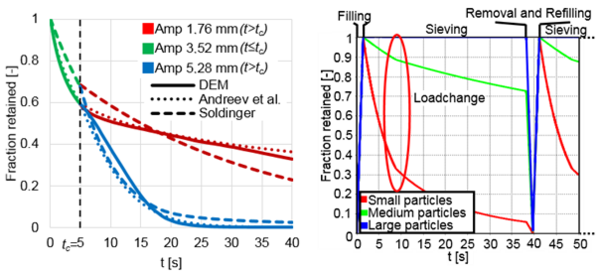
The dependence of the two processes on the operating conditions was analyzed [5] and, based on this, prototypes of dynamic process models were developed and adapted to DEM simulations. Existing models in the literature served as starting points for the development of the dynamic process models. Based on discontinuous sieving processes, continuous processes [6-8] were considered in which transport of the particles along the screen is of significance in addition to segregation and particle passage (see Figure 1). The influence of stationary and time-varying operating conditions on the relevant sub-processes was derived from DEM simulations and also integrated into dynamic process models [9], which were developed based on existing models from literature and which will be further optimized. The applicability of the phenomenological screening models to represent dynamic processes during DEM screening simulations could be confirmed [10] (see Figure 2).
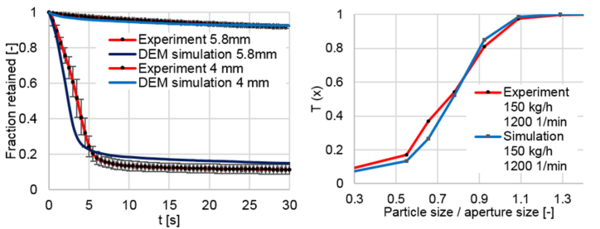
A method to determine DEM parameters for spherical and non-spherical particles easily and reliably was developed, which are first determined by single particle characteristics and then optimized by an adjustment of simulations to small-scale experiments with an automatic algorithm [11]. Furthermore, the particle shape influence could be analyzed by means of a new method for automatic shape approximation. Comparative evaluations with regard to experimental investigations applying model and real particle shapes on own discontinuously operated screens [10,11] as well as on continuously operated screens of project partners (RG Teipel) were performed [12,13]. Additionally, numerical comparisons were carried out based on experiments of a deflector adsorber of RG Weber, whereby a good agreement was obtained and the applicability for further investigations could be ensured [13].
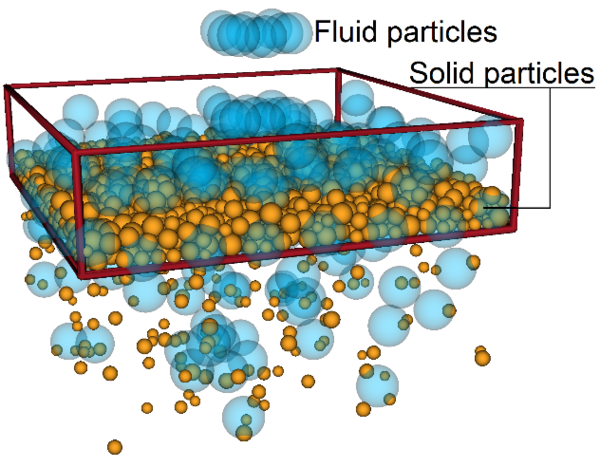
The applied DEM framework was simplified by periodic boundary conditions and optimized for run-time. At the moment, the influence of moisture content on the screening process is investigated and included in dynamic screening process models. In the following, wet screening will also be considered (compare Figure 4), whereby the influence of fluids on the discontinuous and continuous screening process are investigated with the experimentally (own experiments and of RG Kwade) validated DEM / SPH method and the obtained parameters are used for the phenomenological screening models which are integrated in the dynamic flowsheet simulation. In addition, these models are extended with predictive properties and interconnections of comminution and classifying processes are tested (RG Kwade, RG Weber and others).
Collaborations with other projects of SPP 1679
RG Fritsching, Research topic: Process modeling for dynamic dispersed classification and separation processes; Collaboration: Exchange of information and material analysis
RGs Kwade and Schilde, Research topic: Dynamic process models for fine grinding and dispersing; Collaboration: Experimental validation and conjunction of process chains
RGs Scherer and Specht, Research topic: Experimental and numerical analysis for the derivation of a dynamic solid bed model in rotary drums considering mixing and segregation processes; Collaboration: DEM framework based on the same DEM code
RGs Teipel and Weber, Research topic: Dynamics of separation characteristics of sieving and flow classification processes; Collaboration: Close exchange of experimental and numerical data as well as coordination during model derivation
RG Schmidt (Wuppertal), Research topic: Property function for evaluation of dustiness of powders; Collaboration: Integration of determined particle properties (dustiness)
RG Schmidt (Ulm), Research topic: Stochastic particle models – Quantification of relationships between process parameters, structural characteristics and material properties; Collaboration: Provision of representative particle trajectories from the DEM
RG Heinrich, Research topic: Central project: Dynamic simulation of interconnected processes; Collaboration: Integration of phenomenological screening models into the central project
Publications
[1] Kruggel-Emden H., Elskamp F., 2013, Modeling Real Granular Screening Processes of Non-Spherical Particles, 13th European Symposium on Comminution & Classification ESCC, Braunschweig, Deutschland.
[2] Kruggel-Emden H., Elskamp F., 2014, Modeling of Screening Processes Involving Non-Spherical Particles, Chemical Engineering & Technology 37 (5), 847–856. (DOI: 10.1002/ceat.201300649)
[3] Elskamp F., Kruggel-Emden H., 2015, Review and benchmarking of process models for batch screening based on discrete element simulations, Advanced Powder Technology 26 (3), 679-697. (DOI: 10.1016/j.apt.2014.11.001)
[4] Elskamp F., Kruggel-Emden H., Komossa H., Scherer V., Hennig M., Teipel U., 2014, A comparative study of phenomenological screening process models based on discrete element simulations, 7th World Congress on Particle Technology, Peking, China.
[5] Hennig M., Elskamp F., Kruggel-Emden H., Teipel U., 2014, Dynamisch-physikalische Modellierung von Siebklassierprozessen, Chemie Ingenieur Technik 86 (9), 1566. (DOI: 10.1002/cite.201450646)
[6] Kruggel-Emden H., Elskamp F., 2014, Numerical Investigation of a Continuous Screening Process by the Discrete Element Method, 12th International Conference of Numerical Analysis and Applied Mathematics, Rhodos, Griechenland.
[7] Elskamp F., Kruggel-Emden H., Hennig M., Teipel U., 2015, Numerical Investigation of Banana Screens Involving Non-Spherical Particles by the Discrete Element Method, 8th International Conference for Conveying and Handling of Particulate Solids, Tel-Aviv, Israel.
[8] Elskamp F., Kruggel-Emden H., Hennig M., Teipel U., 2015, Benchmarking of process models for continuous screening based on discrete element simulations, Minerals Engineering 83, 78-96. (DOI: 10.1016/j.mineng.2015.08.011)
[9] Elskamp F., Kruggel-Emden H., Hennig M., Teipel U., 2016, Discrete element investigation of process models for batch screening under altered operational conditions, Powder Technology 301, 2016, 78-95. (DOI: 10.1016/j.powtec.2016.05.039)
[10] Elskamp F., Kruggel-Emden H., Hennig M., Teipel U., 2016, Applicability of phenomenological screening models in representing dynamic processes during DEM screening simulations, Partec 2016, Nürnberg, Deutschland.
[11] Hennig M., Elskamp F., Teipel U., Kruggel-Emden H., 2016, Experimentelle Siebklassierung und deren Abbildung in der DEM, Chemie Ingenieur Technik 88 (9), 1363. (DOI: 10.1002/cite.201650046)
[12] Elskamp F., Kruggel-Emden H., Hennig M., Teipel U., 2016, A strategy to determine DEM parameters for spherical and non-spherical particles, 19:46. (DOI: 10.1007/s10035-017-0710-0)
[13] Spötter C. Elskamp F., Hennig M, Teipel U., Weber A.P., Kruggel-Emden H., 2016, DEM-Simulation der Trennkurven in Siebung und Gegenstromsichtung bei geringen Gutbeladungen, Chemie Ingenieur Technik 89, 1726–1738. (DOI: 10.1002/cite.201600156)
[14] Markauskas, D., Elskamp F., Kruggel-Emden H., 2017, Investigation of procedures required for modelling of wet sieving using the coupled DEM-SPH method, Particles 2017, Hannover, Deutschland.
[15] Elskamp F., Kruggel-Emden H., 2017, DEM simulations of screening processes under the influence of moisture, 10th World Congress of Chemical Engineering, Barcelona, Spanien.
[16] Elskamp F., Kruggel-Emden H., 2018, DEM simulations of screening processes under the influence of moisture, Chemical Engineering Research and Design 136, 593-609. (DOI:10.1016/j.cherd.2018.06.022)
[17] Elskamp F., Kruggel-Emden H., 2018, Extension of process models to predict batch screening results under the influence of moisture based on DEM simulations, Powder Technology, eingereicht.