Dynamic Simulation of the Mechanical Fluid Separation in Centrifuges
- Institut:
Institute for Mechanical Process Engineering and Mechanics, Karlsruhe Institute of Technology (KIT)
- Project manager:
- Editor:
Project goal
In many cases, particle generation by crystallization, precipitation or synthesis takes place in the liquid phase. For better storage or processing, it is often necessary to separate the disperse solid from the liquid phase. For this purpose, mechanical liquid separation by means of static thickeners, filters or centrifuges is used. For nanoscale or micron particle systems, solid bowl centrifuges that generate a multiple of the acceleration due to gravity are particularly suitable. Here, centrifuges have the task of ensuring clarification, classification, sorting or mechanical dewatering. For reasons of resource and energy efficiency, complete dewatering of the particulate product is achieved by combining mechanical and thermal drying. The difficulty in the development of physically based process models for the separation step of centrifugation is the spatial and temporal change of the product properties such as particle size, particle size distribution, and particle shape but also physico-chemical properties. In addition, centrifuges are semi-batch and continuous apparatuses, which mean that knowledge of the flow conditions is essential for efficient process modelling. The aim of this project is the formulation of a physically based process model for the dynamic simulation of solid-liquid separation in real time. Here, the separation processes in different centrifuge types such as beaker centrifuges, tubular centrifuges and decanter centrifuges are mapped using a compartment approach. The compartment model represents the internal scheme of the process, which allows the temporal and spatial resolution of material properties such as sedimentation behaviour, heap formation and sediment transport. For the dynamic modelling of solid bowl centrifuges, computationally efficient process models have to be developed, which make it possible to map a large time scale of several hours in a short time. This circumstance requires a model reduction of the existing equation system as well as the development of models representing the flow conditions in centrifuges.
Work program
In the first part of the project characterization methods are to be developed which allow investigating the separation properties of sedimentation, cake formation and transporting behaviour on a laboratory scale. The data obtained will be used to derive the material functions for the process model. In the next step, the coupling of the material functions with the system behaviour of solid bowl centrifuges takes place. For this purpose, it has to be examined whether there is a correlation between system behaviour and residence time behaviour and whether a master curve can be derived for the machine function. Here, three methods are used for these investigations: experimental residence time measurement, analysis of system behaviour and computational fluid dynamics (CFD). The machine function is investigated for a counter-current decanter centrifuge on a pilot scale. In the further course, the linking of the separating material functions and the machine function is to be worked out. For this purpose, a numerical algorithm will be developed which allows a spatially and time-resolved simulation of decanter centrifuges. Another important focus is the experimental validation of the new dynamic model. For this purpose, experiments for separation, classification and mechanical dewatering will be carried out on a pilot-scale decanter centrifuge. In order to verify the transferability of the approach to other centrifuge types, the dynamic modelling of tubular centrifuges based on the compartment approach for counter-current decanter centrifuges is carried out in a further step. In contrast to decanter centrifuges, nanoscale particulate systems such as titanium dioxide or silica are in the foreground. Finally, the dynamic process models are to be integrated into Dyssol and an interconnection of individual basic operations will be realized. For this purpose, the interconnection of the precipitation of barium sulfate in a continuous stirred reactor with different centrifuge types is investigated in order to show the time-efficient calculation of the models on the one hand and to additionally consider the overall dynamics of the interconnected process.
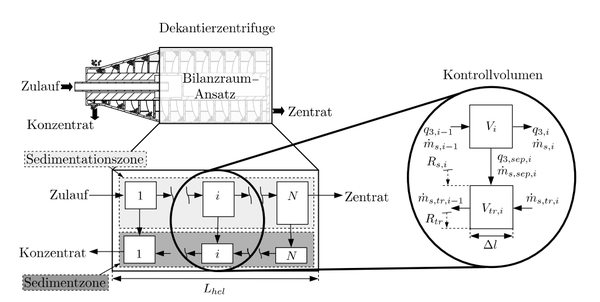
Project-based publications
1. M.Gleiss, H. Nirschl: Modeling separation process in decanter centrifuges by considering the sediment build-up, Chemical Engineering & Technology, (2015), Volume 38, Issue 10, 1873-882
2. M.Gleiss, SHammerich, M. Kespe, H. Nirschl: Application of the Dynamic Flow sheet Simulation Concept to the Solid-Liquid Separation: Separation of Stabilized Slurries in Continuous Centrifuges, Chemical Engineering Science, (2017), Volume 163, 167-178
3. M. Gleiss, S. Hammerich, M. Kespe, H. Nirschl: Development of a Dynamic Process Model for the Mechanical Fluid Separation in Decanter Centrifuges, Chemical Engineering & Technology, (2018), Volume 41, Issue 1, 19-26
4. M. Gleiß: Dynamische Simulation der Mechanischen Flüssigkeitsabtrennung in Vollmantelzentrifugen, Dissertation, (2018), Karlsruher Institut für Technologie
5. S. Hammerich, M. Gleiß. H. Nirschl: Modellierung und Simulation von Vollmantelzentrifugen als ein Aspekt der voranschreitenden Digitalisierung in der Fest/Flüssig Trennung. Chemie Ingenieur Technik, (2019), Volume 91, Issue 3, 215-227