Dynamic Flowsheet Simulation of Solids Processes for Chemical Looping Combustion
Introduction
Interconnected fluidized bed reactors play an important role in a variety of industrial applications, like Partial Oxidation (POX), Fluid Catalytic Cracking (FCC) and Chemical Looping Combustion (CLC). In these processes, a reactive material is looped between two reactors, being used in the first and regenerated in the other.
The exemplary CLC is a carbon capture process, where carbon dioxide is separated from flue gases via this system of fluidized bed reactors. Between these two fluidized bed reactors oxygen carrying (OC) material is circulated, taking in oxygen in an air reactor, releasing it in the fuel reactor.
For modelling of this strongly coupled system, a dynamic flowsheet simulation environment is applied. For capturing dynamic effects within the system like load alternation, attrition and startup as well as shut-down procedures, simpliĀfied models are derived and experimentally evaluated and parameterized.
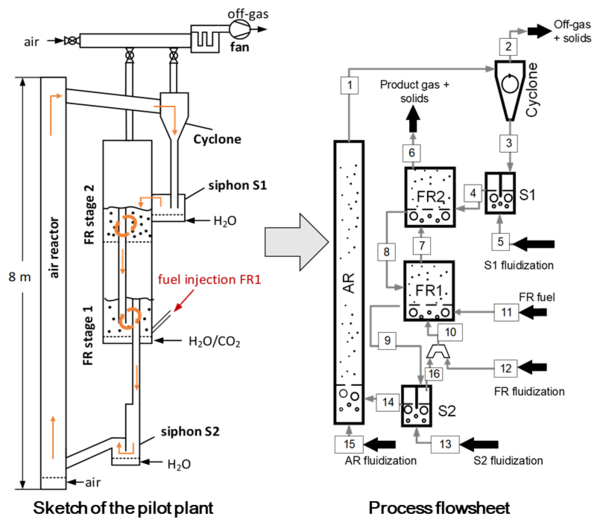
Aims of the projects
A novel flowsheet simulation environment called DYSSOL is developed that is able to capture dynamic effects within solids processes. In addition to that, distributed properties for several particle fractions can be handled.
Reactor and equipment models for the CLC process will be implemented into this simulation environment to investigate the reactor system and its behavior during combustion. The models have to be evaluated and validated experimentally. The validated models will then be used to simulate dynamic effects, like fuel load alternation and shut-down and start-up procedures.
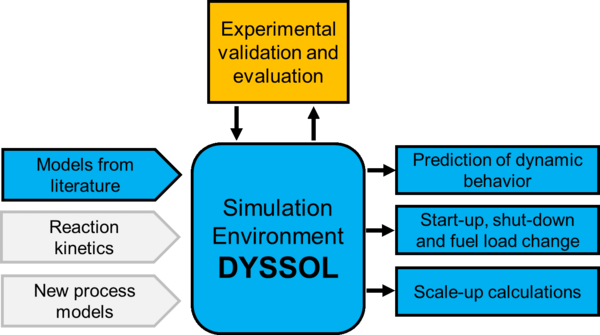
Methods
The basic approach for developing an accurate Flowsheet simulation is the implementation of suitable empiric and semi-empiric hydrodynamic models for the fluidized bed reactors from literature. Exemplary models are the model from Werther and Hartge (2003), applied for the air reactor, and from Werther and Wein (1994) for the bubbling fluidized bed fuel reactor. Chemical reactions are calculated by overall kinetic reaction scheme developed for Chemical Looping Combustion of solid fuels. Therefore, the interaction of bubble and suspension phases inside the reactors are included.
Various experiments on pilot as well as lab scale facilities are carried out to parameterize the models and create experimental data for reaction network and chemical kinetics.
Experimental setups
The experimental validation is carried out at the experimental Chemical Looping facility of 25 kWth rated power, which is operated at the TUHH. The schematics of the two-stage fuel reactor system are shown in Figure 1. The two-stage system was demonstrated to be able to convert volatiles and gasifying the fuel char. Very high conversions of bituminous coal, lignite and biomass were observed with a CuO/Al2O3 oxygen carrier.
Furthermore, reactivity measurements can be carried out in a small lab scale fluidized bed facility.
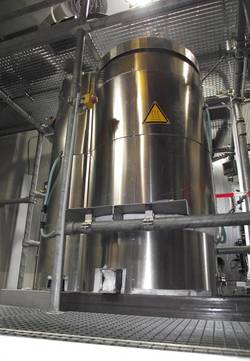
Selected Publications
Haus, J., Hartge, E.-U., Heinrich, S.; Werther, J. (2018) Dynamic flowsheet simulation for chemical looping combustion of methane - International Journal of Greenhouse Gas Control, 72:26-37