Impact comminution in jet mills
- Institute:
Institute of Particle Technology (LFG) , FAU Erlangen-Nürnberg
- Procect leader:
Prof. Dr.-Ing. habil. K.E. Wirth, FAU Erlangen-Nürnberg
Prof. Dr.-Ing. W. Peukert, FAU Erlangen-Nürnberg- Researcher:
M.Sc. B. Köninger, FAU Erlangen-Nürnberg
Dr.-Ing. H. Förster, FAU Erlangen-Nürnberg
Introduction and project goals
In jet mills, solid particles are comminuted with the aid of highly expanded gas jets. To achieve this, the particles are accelerated to high velocities. If these particles collide with each other, the involved particles can break. The probability of two particles colliding (impact probability) and the kinetic energy of the collision partners (being greater than the energy required for triggering the particle fracture) are decisive for the comminution. Since the particles are grinded autogenous, advantages are obtained for the comminution process, e.g. a low wear of the device, as well as a nearly contamination-free grinding of very hard materials. Due to the high specific energy requirement, the use of this mill type is limited to fine grinding. The comminution of the particles takes place in the region of the gas jets in the lower part of the jet mill. The grinding gas transports the material present in the mill to the upper region of the mill, where the fine material is separated by a classifier wheel and leaves the mill. The coarse material rejected by the classifier wheel drops down into the grinding zone, where it can be impacted again in the region of the gas jets (see Figure 1). Three fundamental operations of the mechanical process technology are therefore interlinked in the jet mill: comminution in the region of the gas jets, pneumatic transport of solids from the grinding zone to the classifier wheel and the classification by a dynamic classifier wheel.
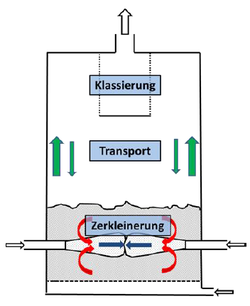
In jet mills, this results in a highly integrated interaction of the unit operations, which has an effect on the particle size distribution of the comminuted material, as well as on the throughput of the solid mass flow, especially during start-up and shutdown of the mill.
For the prediction of processes in mills, it has been proven successfully to subdivide the description of the mill into an apparatus (in this case mill) and a material function (see Figure 2) [1]. The former describes the stressing conditions delivered by the fluid mechanic of the mill. With this apparatus function, the motions of the particles relevant for comminution can finally be calculated. The material function, on the other hand, describes the influence of the particle movement on the comminution process as a function of the material parameters. The combination of apparatus and material function allows the prediction of the breakage probability for different solid materials. Therefore, knowledge of apparatus and material function is necessary for flow sheet simulations. Preliminary work by Vogel [2] showed that it is thus possible to transfer the findings from single-particle impact tests to impact mills.
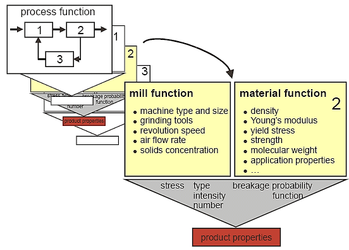
The aim of the project is to model the dynamic behavior of opposed jet mills by means of experimental investigations. In addition to the experimental investigation of the operating behavior of jet mills, a model of the comminution process will be developed in a time-dependent manner. This module will be implemented in Dyssol for the dynamic simulation. In order to achieve this goal, models for the apparatus function of the mill as well as the material function are to be developed, in order to create a mill model which allows the prediction of the processes in jet mills and can be integrated into the simulation of cross-linked solid processes.
Work schedule
The apparatus function is to be systematically examined for its dynamic behavior. The solid hold-up, which adjusts itself in the mill, plays a central role. The discharged product mass flow as well as its fineness is influenced by the hold-up. For this reason, the incoming and outgoing solid mass flows as well as the particle size distributions at the mill outlet are measured online. Thus, an integral characterization of the dynamic behavior of the mill is possible. The experimental setup also makes it possible to investigate the influence of the three basic operations (comminution, solids transport, and classification) for the entire grinding process. Thus, e.g. the comminution can be viewed individually by stopping the classifier wheel while the discharged solid is separated in a cyclone. Toneva [3] was able to prove a decoupling of the grinding and classification zone in a pin mill with integrated classifier. This situation is also to be proven in jet mills. Part of the investigations is also the geometry of the grinding chamber and nozzles, which are varied by different designs. The solids distribution in the mill and in particular in the grinding zone should be measured in a high-resolution manner. A highly loaded gas-solid flow is present in jet mills. The classification of the ground solid requires high circumferential speeds, which lead to a vortex flow in the mill, resulting in forming of strands. They are deposited at the mill wall before reaching the classifier and even product sized particles then are rejected. This results in high fines content in the mill. The influence of the classifier on the multi-phase flow in the mill is to be systematically investigated by changing the mill geometry in the area between the grinding zone and the classifier. The fluid mechanics within the mill, in turn, has a reaction to the flow state in the gas flow and thus to the efficiency of the comminution in the grinding zone. The grinding zone itself is selectively modified by using different (supersonic) nozzles, as well as by the local position of the nozzles in the lower region of the mill.
In addition to the apparatus function, a model for the material function is to be developed. For this purpose the breakage probability and the breakage function of different materials are determined in order to create predictive models. Previous apparatuses for impacting single particles work in a particle size range greater than 25 μm [4]. However, since particle sizes below 1 μm are achieved in jet mills, a new apparatus is constructed in which particles are to be stressed up to the nanometer scale by impact. Unknown material data such as hardness and fracture toughness, which are essential for the modeling, should be determined by means of indentation experiments. Meier [5] showed that the material parameters of the particle fracture are influenced by the plastic properties of the material. In addition, the material parameters are determined by means of mechanical experiments with a SEM supported manipulation device, which are used in the predictive models.
Results of the 1st & 2nd funding periode
Group of Prof. Wirth
In the first two funding periods, the fluid mechanics of the comminution process was investigated and characterized. The comminution in the jet mill can be described and modeled with the stressing frequency and intensity in the high-turbulent multi-phase jets. The fluidized bed with secondary gas injection serves as a model, which, however, is operated conventionally (usually) with more moderate gas velocities (and correspondingly lower fracture rates). A semicircular fluidized bed in combination with a glass plate was used to determine particle velocities. This provides an optical access to the flow from the nozzle, which has also been manufactured in the semicircular format. The analysis of the jet is done by using PIV (particle image velocimetry). Figure 3 a) shows a velocity field. It is shown that the maximum particle velocities are reached close to the jet axis. Using the single-phase free jet theory, a simplified particle velocity as a function of the dimensionless nozzle distance X d0-1 can be calculated by means of a force balance. The measured values can thus be described well as a first approximation, as shown in Figure 3b).
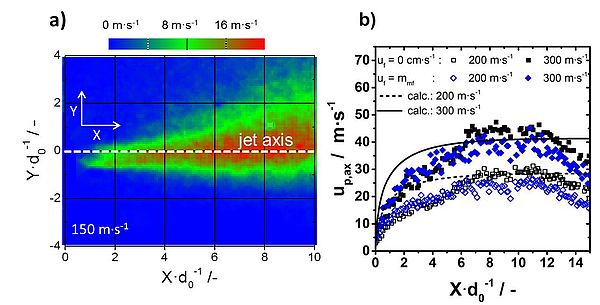
The injection behavior from the nozzle was also simulated numerically (single phase) for various parameters (gas velocity, nozzle diameter d0, ...) with Ansys Fluent. With these data, particle trajectories are determined via a one-way coupling, as can be seen in Figure 4. Thus, it is possible to calculate breakage probabilities PB based on the model of Peukert [1]. This is also shown in Figure 4 for two different fracture scenarios. With this approach, it is now possible to couple the fluid mechanics of the mill with the individual fracture behavior of particles. This methodology is to be pursued further and implemented in the framework system Dyssol.
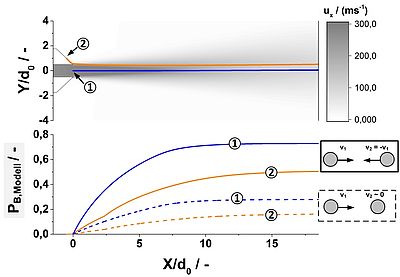
In addition to the stress intensity, the stress frequency is also important for the determination of a breakage rate. For this purpose, the concentration of solids in the jets was investigated using capacitive probes. A disadvantage of the probes is the disturbance of the flow as well as a high wear caused by the particles. For this reason, a fluidized bed was scanned by X-ray computer tomography. Figure 5 shows a schematic measurement setup including scans at different measuring heights.
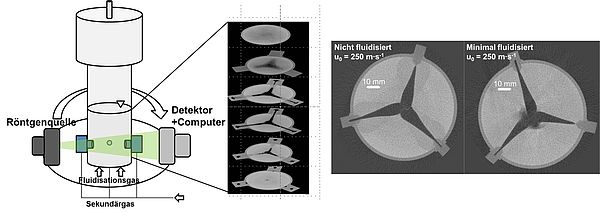
In the future, this non-invasive measurement technique will be used to determine the concentration of solids in different areas of the jet. Thus, the stress conditions of the particles in the grinding chamber of the mill can be better described.
In addition to fluid mechanics, the process dynamics were examined in a laboratory jet mill (Alpine AFG 100). The main goal was the determination of the grinding kinetics at different operating conditions. It was clear that, besides the particle size distribution, the holdup in the mill plays a decisive role. Depending on the material properties, there is an optimum load in the mill to achieve a high breaking rate. For this reason, the holdup within the mill was one of the main parameters for the fluid mechanical investigations in order to depict the process dynamics.
Group of Prof. Peukert
Material function
In the promoted period, the low-pressure impact device (Figure 6) required to determine the breakage probabilities and breakage functions for particles smaller than 25 μm was designed, built, and put into operation. The particles are fed via a dispersing unit at the upper end of the vertical acceleration path. After passing through the accelerating path, the particles hit the impact plate (aluminum oxide, E = 360 GPa), whereby the plate spacing to the exit point and the impact angle can be varied. The different impact angles, as known from the fluidized-bed opposed jet mill, can thus be simulated and characterized in a simplified manner.
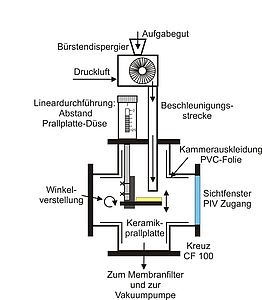
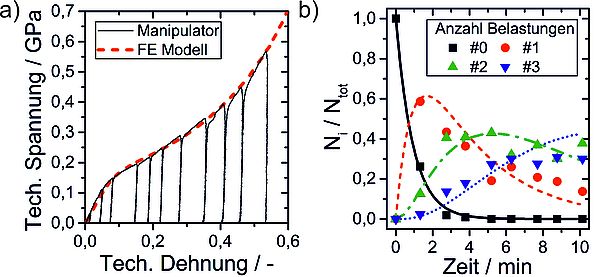
Particle image velocimetry (PIV) was used for the first flow mechanical characterization: particles up to 20 μm in size can be accelerated to speeds of up to 300 m/s. In addition, breakage probabilities were determined for the materials limestone, alumina and glass.
The mechanical characterization of the feed materials used for the investigation of the one- and two-sided particle stressing is carried out by means of an SEM-supported micromanipulation device. The obtained force-displacement data was used to extract mechanical parameters for the material function and to validate a FE model for the two-sided stressing of particles (Figure 7a)).
Apparatus function
By evaluating characteristic geometric ratios for a significant number of particles from experiments in the stirred media mill, the degree of deformation and thus the distributions of the effective stress energy could be determined. The additional evaluation of the number of contacts/stresses per particle enabled the development of stress kinetics (Figure 7b)). The established method for determining the stress energy and number [6] is to be transferred to the case of one-sided stressing in the low-pressure impact device unit and the fluidized bed opposed jet mill, and the results are integrated into the simulations of the project partners.
Work schedule of the individual groups for the third funding period:
Group of Prof. Wirth, FAU Erlangen-Nürnberg
-
Analysis of the process dynamics
-
Local determination of the solids mass distribution in the mill (grinding zone/transport/classifier)
-
Scale-up to AFG 200: comparison of grinding kinetics
-
Fluid dynamics in the gas jet
-
Determination of the solids mass distribution using high-resolution X-ray computer tomography
-
Recording of particle trajectories using a high-speed camera and alignment with simulation
-
Improvement of the shortcut model
-
Implementation of other materials
-
Consider of the stress number and the residence time in the mill
Group of Prof. Peukert, FAU Erlangen-Nürnberg
-
One-sided stressing
-
Determination of the breakage function and breakage probability for monodisperse glass spheres, hard materials, polymers, organic crystals (dp < 40 μm)
-
Form analysis of metal particles as a function of impact energy and impact angle and transfer to the jet mill
-
two-sided stressing
-
Determination and description of the mechanical behavior in the SEM manipulator and the FEM simulation
-
Development of material functions
-
Dependency of the SN/SE distribution of operating parameters (speed, grinding ball size, …)
-
Stress number in the jet mill
-
Use of mixed hard material/metal particle systems
-
Determination of the stress number in the jet mill from statistical image analysis
Literature
-
W. Peukert, L. Vogel, Comminution of polymers-an example of product engineering, Chemical Engineering and Technology 24 (9) (2001) 945-950
-
L. Vogel, W. Peukert, From single particle impact behaviour to modeling of impact mills, Chemical Engineering Science 60 (2005) 5164-5176
-
P. Toneva, K.-E. Wirth, W. Peukert, Grinding in an air classifier mill – Part II: Characterization of the two-phase flow. Powder Technology 211 (1) (2011) 28-37
-
M. Meier, Development of predictive tools for the characterization of milling behavior of pharmaceutical powders, Ph.D. Thesis, Universität Erlangen (2010)
-
M. Meier, E. John, D. Wieckhusen, W. Wirt, W. Peukert, Influence of mechanical properties on impact fracture: Prediction of the milling behaviour of pharmaceutical powders by nanoindentation, Powder Technology 188 (2009) 301-313
-
A. Strobel, S. Romeis, S. Wittpahl, P. Herre, J. Schmidt, W. Peukert, Characterization of stressing conditions in mills – A comprehensive research strategy based on well-characterized model particles, Powder Technology 305 (2017) 652–661.