Investigation of the dynamic behavior of spray granulation in continuously operated multi-staged horizontal fluidized beds
- Institutions:
Institute of Solids Process Engineering and Particle Technology, Hamburg University of Technology
Chair of Automation and Modelling, OvGU Magdeburg
Chair of Thermal Process Engineering, OvGU Magdeburg- Project leader:
Prof. Dr.-Ing. habil. S. Heinrich, Hamburg University of Technology
Prof. Dr.-Ing. habil. Dr. h.c. A. Kienle, OvGU Magdeburg
Prof. Dr.-Ing. habil. E. Tsotsas, OvGU Magdeburg- Project manager:
M.Sc. E. Diez, Hamburg University of Technology
Dipl.-Ing. C. Neugebauer, OvGU Magdeburg
M.Sc. K. Meyer, OvGU Magdeburg
Motivation
This research project aims at a detailed investigation of the complex process dynamics arising in continuously operated multi-stage fluidized bed granulation. This process has prototypic character for the dynamic simulation of coupled particle processes, due to the presence of different process chambers, the presence of zones with different functionality in each process chamber, the high flexibility in designing the internal coupling between different chambers and zones with different classification characteristics, the coupling between particle and fluid phase due to drying, varying positions and classification characteristics of external recycles, and multiple internal coordinates to characterize product properties. Consequently, the project follows a multi scale approach, which combines experimental work with different modeling methods and a nonlinear analysis of process dynamics.
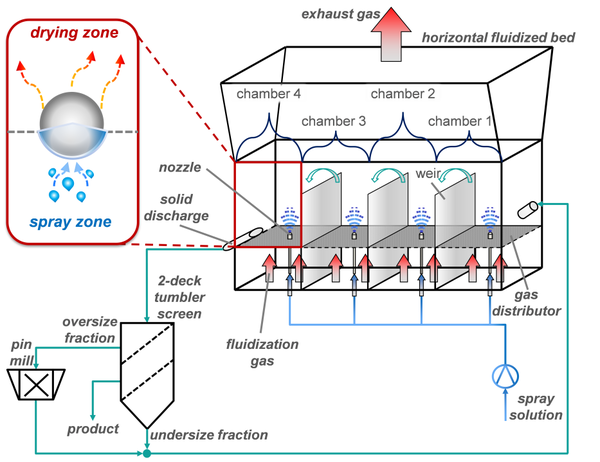
Work schedule
Experiments for the multi-chamber fluidized bed granulator will be done by the Heinrich group. Further, this group applies discrete particle modeling (DPM) to describe the dynamics of particle transport between different chambers and different functional zones within the chambers, with special emphasis on classification characteristics. Another focus is on the modeling of the periphery for processes with external product classification and recycle.
The Tsotsas group develops population balance and heat and mass transfer models for the description of the temporal evolution of particle properties for different process configurations and different operating conditions, including parameterization of the models. Moreover, this group provides detailed characterization of particle properties (particle size distribution, X-ray micro tomography, scanning electron microscopy, mechanical stability) as well as novel particle tracking velocimetry experiments for investigation of particle transport at weirs.
The Kienle group is concerned with the development of new methods for system and parameter identification and system theoretical analysis of the nonlinear dynamic behavior of continuous multi-chamber fluidized bed granulation. The analysis provides further insight into the underlying processes. In cooperation with the other groups, results will be used for an evaluation, refinement and discrimination of the developed population balance modeling approaches. Auto tuning controllers will be developed to speed up the time consuming experiments. These will be combined with suitable methods for prediction and detection of possible open loop instabilities and implemented at the plant.
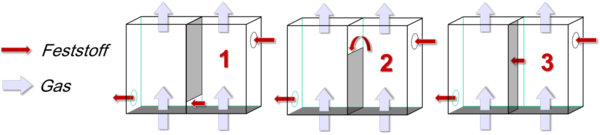
Project cooperation
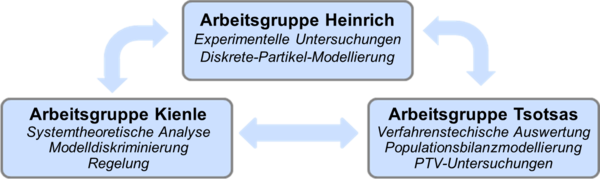
Publications
• Bück, A., Neugebauer, C., Meyer, K., Palis, S., Diez, E., Kienle, A., Heinrich, S., Tsotsas, E., 2016. Influence of operation parameters on process stability in continuous fluidized bed layering with external product classification, Powder Technology 300, 37-45.
• Dreyschultze, C., Neugebauer, C., Palis, S., Bück, A., Tsotsas, E., Heinrich, S., Kienle, A., 2015. Influence of zone formation on stability of continuous fluidized bed layering granulation with external product classification, Particuology 23, 1-7.
• Meyer, K., Bück, A., Tsotsas, E., 2016a. Determination of particle exchange rates at over-flow weirs in horizontal fluidised beds by particle tracking velocimetry, Particuology, in press, DOI: 10.1016/j.partic.2016.09.007
• Meyer, K., Bück, A., Tsotsas, E., 2016b. Multi-compartment model for study of thermal effects during granulation in a continuously operated horizontal fluidized bed, Proceedings of International Drying Symposium (IDS 2016), Gifu (JP).
• Neugebauer, C, Palis, S., Bück, A., Diez, E., Heinrich, S., Tsotsas, E., Kienle, A., 2016a. Influence of mill characteristics on stability of continuous layering granulation with external product classification, Computer Aided Chemical Engineering 38, 1275-1280
• Neugebauer, C., Palis, S., Bück, A., Tsotsas, E., Heinrich, S., Kienle, A., 2016b. A dynamic two-zone model of continuous fluidized bed layering granulation with internal product classification, Particuology 31, 8-14.
• Palis, S., Neugebauer, C., Bück, A., Heinrich, S., Tsotsas, E., Kienle, A., 2016. Control of multi-chamber continuous fluidized bed spray granulation, Proceedings of the International Congress on Particle Technology (PARTEC), April 19-21, Nürnberg.
• E. Diez, K. Meyer, A. Bück, E. Tsotsas, S. Heinrich, 2018. Influence of process conditions on the product properties in a continuous fluidized bed spray granulation process, Chemical Engineering Research and Design 139, 104-115.