Dynamic process models for fine grinding and dispersing
- Institute:
Institute for Particle Technology, Technische Universität Braunschweig
- Project leader:
Prof. Dr.-Ing. Arno Kwade, TU Braunschweig
Dr.-Ing. Carsten Schilde, TU Braunschweig- Research assistant:
Dipl.-Ing. Greta Fragnière, TU Braunschweig
Project goal
A large part of the global energy demand is spent on comminution during the processing of solids in different industries. Fine grinding, i.e. comminution in the lower micrometer and sub-micrometer range, is thereby increasingly gaining importance, not only in the chemical and pharmaceutical industry, but also in mineral processing and ceramics industries. Stirred media mills are especially suited for wet ultra-fine grinding and dispersing.
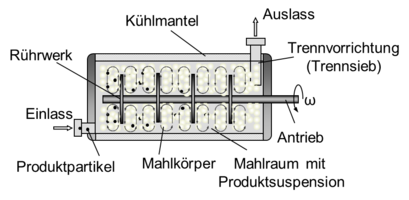
For a predictive model of grinding or dispersing processes considering dynamically changing operating parameters, the distinction between machine and material function is necessary. On the one hand, the process is determined by the fracture properties of particles in the mill feed. On the other hand, there are machine parameters such as the stirrer geometry, the material and size of grinding beads, and the stirrer speed, which significantly affect the grinding or dispersing process. In a continuous process, the volume flow and the control strategy add to the major influencing factors. During wet ultra-fine grinding in stirred media mills the viscosity of the medium may vary with the particle size distribution and concentration of solids. These changes in viscosity influence the grinding bead distribution within the grinding chamber and thus the stress conditions. For dynamic process simulation it is therefore crucial that the machine function is determined by models that incorporate the effects of the operating conditions. Required sub-models are, for example, a transport model, a power consumption model, a material distribution model and a stress model (Figure 2).
In addition an efficient method for the calibration of material parameters for fine grinding is necessary.
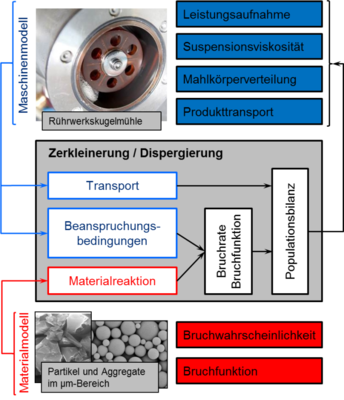
Working Program
Within the first funding phase, the coupling of population balances with physically justified models was used to describe the stressing conditions for discontinuous processes. Two approaches were investigated and compared: The first approach is the Kwade stressing model, which describes the influence of different operating parameters on the mean particle size by means of characteristic values for stressing energy and stressing frequency. The second approach is the investigation of the grinding media contacts via coupled CFD-DEM simulations. In a calibration mill, the breakage rate for different model materials was determined experimentally. The prevailing stressing energy distributions and the stressing frequency were determined using CFD-DEM simulations. In addition, the power consumption at different suspension viscosities and rotational speeds was described using Newton-Reynolds diagrams. The product materials were characterized by micro-compression tests with regard to their fracture probability.
The focus in the second funding period is the continuous process. For the development of a continuous process model, a grinding media distribution model and a product transport model are essential building blocks. The experimental investigations include, amongst others, radiometric density measurements to determine the axial distribution of the grinding media. In addition, the process of trapping and stressing of particles between two grinding beads is examined numerically. For the calibration of material model parameters, a two-roller mill is constructed. By means of spray drying, nanoparticulate aggregates are prepared and then subjected to pressure in order to obtain a model material for dispersing.
Activities of the individual working groups
Working group Kwade, Technische Universität Braunschweig
-
Experimental and simulative (CFD-DEM) characterization of the stressing conditions in a horizontal laboratory stirred media mill
-
Development of a method for calibrating material parameters in the lower μm-range
-
Population dynamics calculation of the comminution process in stirred media mills and incorporation of the model in the flow sheet simulation program Dyssol, which is provided by the Z-project
Working group Schilde, Technische Universität Braunschweig
-
Investigation of the capture probability of product particles between the media by means of CFD-DEM simulations
-
Production of various porous model aggregate structures and determination of a material model for nanoparticular aggregates